Pulp mills are undergoing a clear investment boom – A new mill always requires Finnish expertise
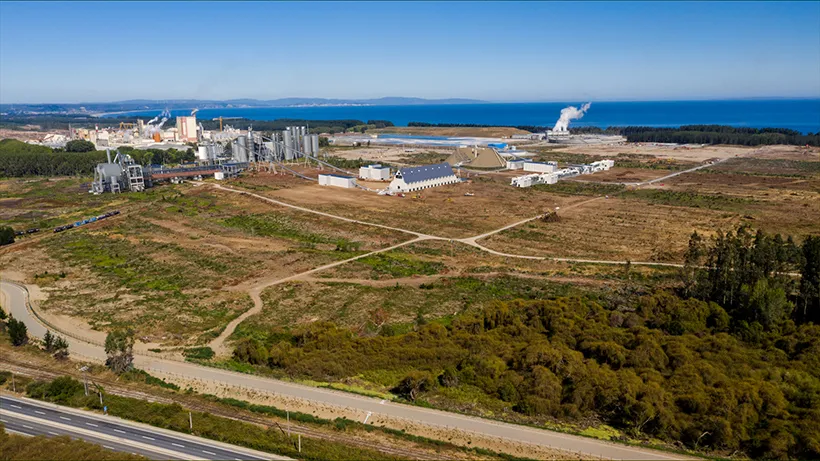
After a brief hiatus, enterprises in the pulp industry are now investing billions of euros in new mills. Each pulp mill has a distinctly Finnish touch to it as Valmet and the Finnish unit of the Austrian Andritz are the only enterprises in the world that can deliver an entire mill to the client. This also provides work for thousands of subcontractors. Finnvera plays a significant role as a provider of financing for investments.
Finnvera’s Finance Manager Satu Savelainen says that there are a lot of pulp and paper projects in the pipeline.
“The next large-scale pulp mill will be completed in Chile in 2021. However, there are numerous mill projects in the pipeline, some of them with existing investment decisions,” notes Savelainen.
Savelainen has been involved in nearly all of the major pulp projects in the world in recent years as Finnvera plays a significant role in the realisation of investments. Whenever and wherever a new pulp mill is built, there is always a Finnish machinery supplier involved.
Pulp makers need the help of export credit agencies in financing their projects as the total costs of new mills may rise to EUR 2–3 billion.
“Our guarantee coverage is typically less than 20 per cent of the project’s total costs. In export credit guarantees, we cooperate with the bank in question,” says Savelainen.
Mill construction projects are concentrated in regions where wood is most readily available: South America, Southeast Asia and the Nordic countries. In addition, old mills are constantly modernised around the world.
South America’s trump card is the quickly growing eucalyptus tree, whereas the strengths of northern softwood include its high quality and sustainability.
“Most of our exposure is associated with South America. In financing decisions, a major due diligence area to be assessed before signing the decision is environmental and social issues. We check, among other things, how subcontractors are treated and how occupational safety has been arranged,” explains Savelainen.
It takes years to build a mill
The world market price of pulp has declined from its highest level but Pellervo Economic Research PTT, for instance, predicts that demand for pulp will continue to grow in the next few years, driven by China.
Pulp is suitable raw material for tissue and other hygiene products, cardboard, packaging materials and, in the form of dissolving pulp, textiles. Furthermore, there are hopes that pulp will replace single-use plastic products.
The pulp mill turnkey suppliers Valmet and Andritz believe in growing demand. This can be seen in the order books.
“The construction of a mill is a long process that can last up to five years. Before the actual investment decision, the concept and technology are discussed with the client. The sales process takes 1–2 years. Planning is one of the most critical phases as all changes in the construction phase complicate the project,” says Kari Tuominen, President and CEO of Andritz Oy.
According to him, the mill delivery time is 2–2.5 years. Purchases from subcontractors are launched as soon as possible. Typically, it takes 6–12 months to achieve the full production level.
"The pulp mill turnkey suppliers Valmet and Andritz believe in growing demand. This can be seen in the order books.
"
Finland has unique expertise
Wood’s journey to pulp consists of many phases, such as the processing of wood, the entire pulp line from pulping to finished bales and the recovery of chemicals. Thanks to automation, all phases form a seamless whole.
In new mills, particular attention is paid to energy efficiency and the utilisation of side streams.
“Managing the big picture is extremely demanding. It is based on the work of thousands of engineers. We take care of the core phases ourselves but we have a network of 10,000 active suppliers,” says Bertel Karlstedt, Valmet’s Business Line President, Pulp and Energy.
Andritz Oy uses approximately one thousand subcontractors, and the entire Andritz Group has a considerably higher number of subcontractors. Both enterprises’ purchases amount to hundreds of millions of euros per year.
It is possible for the client to use expertise from both enterprises as the solutions offered by them are relatively compatible. Karlstedt describes the different elements of a pulp mill as Lego bricks.
“For instance, the deliveries to the Äänekoski bioproduct mill were quite evenly distributed between the enterprises, roughly 50–50,” he comments.
Both Karlstedt and Tuominen find several reasons why Finland has risen to the leading position in the construction of pulp mills.
“We have a long history in the pulp and paper industry. We have believed in the development of the sector and made major investments. Training is absolutely top-notch, and we have great people working for us,” comments Tuominen.
“For Finland, the pulp and paper industry is still the most important export sector. In Finland, the sector, with its various bio product applications, attracts young people, unlike in Germany, for instance, where the sector is not very interesting to them,” Karlstedt goes on to say.
Text: Kimmo Koivikko